
- Stm32 driver stepper motor generator#
- Stm32 driver stepper motor full#
- Stm32 driver stepper motor code#
And the maximum pulse is 12% duty cycle be the same procedure. This division will give you that the minimum pulse 0.6/20 is a 3% duty cycle. Why these numbers? well, the minimum pulse is 0.6ms in width as time, in order to get the duty cycle percentage that represents this pulse width time, we’ll divide 0.6 by 20ms which is the period of the PWM signal (which has a frequency of 50Hz, so it’s period is 20ms).
Stm32 driver stepper motor full#
This means that the entire range of PWM signal that covers the full motor rotation is from 3% up to 12%. Suppose that our servo motor has a minimum pulse width of 0.6ms (for the 0° position) and a maximum pulse of 2.4ms (for the 180° position). That’s a too accurate control signal for such an application and seems more like overkill but let’s continue. This means that the duty cycle has 65536 discrete levels between (0% to 100%). Just imagine that we’ve set up the PWM hardware to generate a PWM signal with a frequency of 50Hz and the duty cycle has a 16-Bit of resolution. The STM32 PWM hardware can go up to 16-Bit 50Hz and we shall seek to get as close as possible to that limit.Īnd here is an example for clarification of the concept of resolution.
Stm32 driver stepper motor code#
Maximizing the resolution will be one of our targets while deriving the equations to be used in code later on. The range of the angle in degrees is from 0 up to 180 will get mapped to whatever values that produces a pulse width between Minimum_pulse and Maximum_Pulse and all depends on the PWM resolution itself. Therefore, the PWM signal’s resolution dictates how fine can we adjust the servo motor’s angle. The angular position of the servo motor is determined by the pulse width of the PWM signal. All in all, it’s not a much of a big deal anyway! But in today’s tutorial, I’ll make a room for these values to be in our code configurations and to take effect. In a previous tutorial, I’ve assumed that the minimum pulse is 0.6ms and the maximum pulse is 2.4ms in order to make everything as simple as possible and not trying to be a perfectionist about it. This picture shows what are the values I’ve got for a different 4 servo motors, and I preferred to label them.
Stm32 driver stepper motor generator#
A quick characterization with a DDS function generator and a DSO has given me the exact figures for the min & max pulse widths (in ms). Other than that, the practical experimentation didn’t only give me the exact pulse widths that correspond to (0° & 180°) but it also proved that those little motors are not the same. Unfortunately, “The datasheet” found on the internet seems to be a poorly translated Chinese paper with a little bit of information about the control signal specs and it turned out to be false. The servo motor that I’ve in my LAB and will be using today is the micro servo with metal gear MG90s. The datasheet for each stepper motor has to have the exact specifications for the pulse width that corresponds to the minimum angular position (0°) it’s called Minimum_Pulse and the pulse width that corresponds to the maximum angular position (180°) and we’ll call this the Maximum_Pulse. To control the position (angle) of the servo motor’s shaft, you’ll have to generate a PWM signal that has a frequency of 50Hz and a variable duty cycle. Affiliate programs and affiliations include, but are not limited to, the eBay Partner Network (EPN) and. Logic Analyzer (on ) ( on eBay)Īffiliate Disclosure: When you click on links in this section and make a purchase, this can result in this site earning a commission.FeelTech DDS Function Generator: KKMoon FY6900 (on ) ( on eBay).My Digital Storage Oscilloscope (DSO): Siglent SDS1104 (on ) ( on eBay).Some Extremely Useful Test Equipment For Troubleshooting: ★ Check The Full Course Complete Kit List
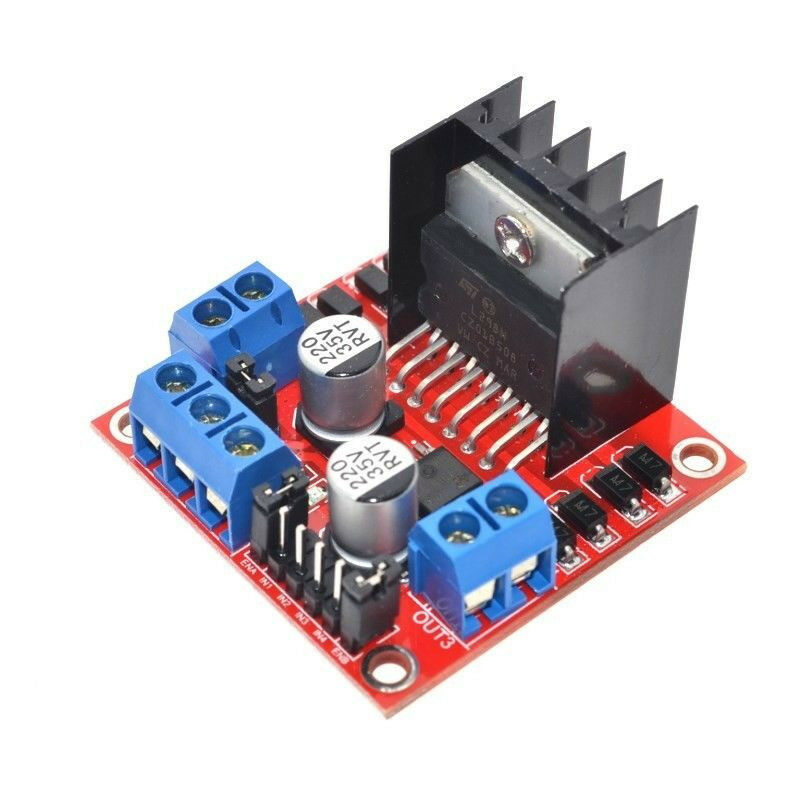
ST-Link v2 Debugger or ( eBay) QTY Component Name 🛒 🛒 2 BreadBoard Amazon eBay 1 LEDs Kit Amazon Amazon eBay 1 Resistors Kit Amazon Amazon eBay 1 Capacitors Kit Amazon Amazon eBay & eBay 2 Jumper Wires Pack Amazon Amazon eBay & eBay 1 9v Battery or DC Power Supply Amazon Amazon Amazon eBay 1 Micro USB Cable Amazon eBay 1 Push Buttons Amazon Amazon eBay 1 Potentiometers Amazon Amazon eBay 4 Micro Servo Motor (Metal Gear) Amazon eBay.Blue Pill STM32-F103 (ARM Cortex-M3 72MHz) or ( eBay).Nucleo32-L432KC (ARM Cortex-M4 80MHz) or ( eBay).8 One Last Testing For STM32 Servo Driver Īll the example code/LABs/projects in the course are going to be done using those boards below.7 STM32 Multi Servo Motors Control – LAB.6 STM32 Analog Servo Motor Control + Knob LAB.
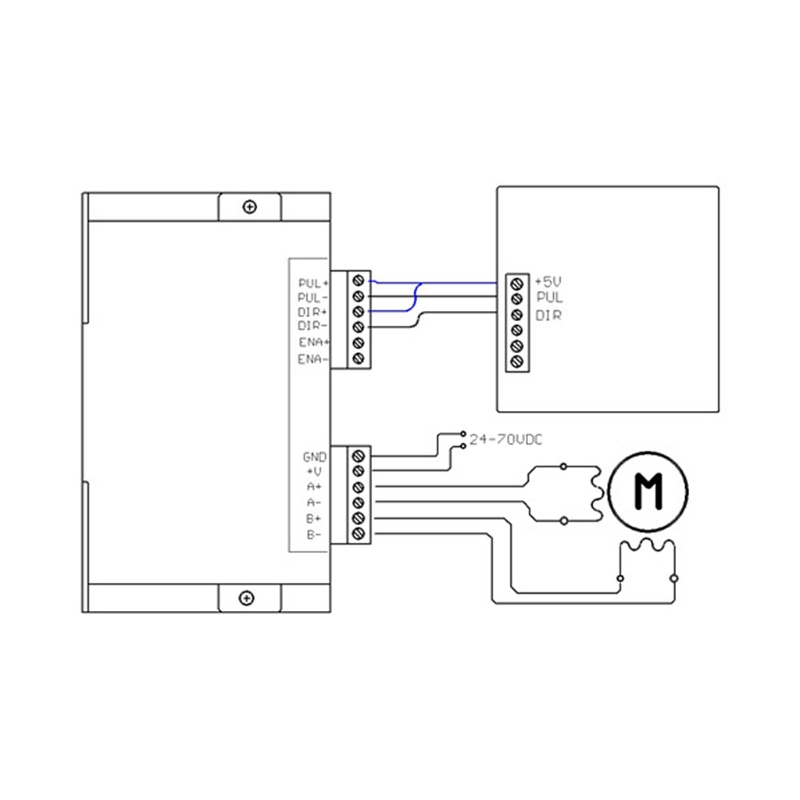

5 STM32 PWM Servo Motor Control – Basic LAB.
